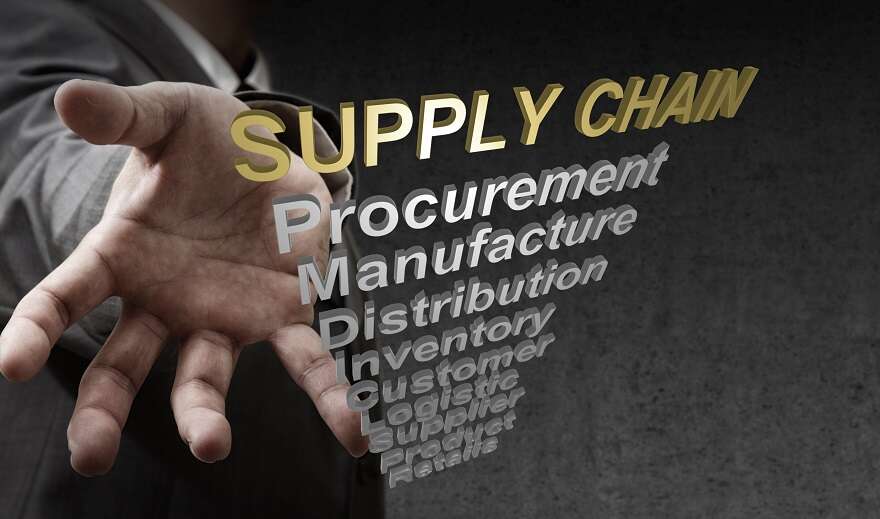
Supply chains can’t afford to be caught short in a crisis again, so what do they need to do to ensure continuity?
“Only when the tide goes out do you discover who has been swimming naked.” Warren Buffet’s famous quote is a perfect description for the current state of service supply chains. The ‘new normal’ has fast become a well-worn phrase during the Covid-19 crisis. Much of it tends to refer to new ways of working; how organisations are going to cope with social distancing and flexible working practises, for example.
But what does this mean to supply chains? The pandemic has been an awakening. In many ways it has exposed supply chains, the often complex, cross-border, inter-industry relationships that have been built up over decades. Over 90 percent of the Fortune 1000 have apparently been affected by supply chain disruption in the past few weeks and the question that most will have asked themselves is could they have done more pre-pandemic to ensure greater resilience in a crisis?
The answer of course is ‘yes’. The old normal should have involved emergency contingency plans and stress testing to ensure continuity but a mix of streamlining, old processes and perhaps even complacency has undermined supply chains. This has led to absenteeism during the current Covid-19 crisis, as Gartner reports in its study on the Coronavirus and impact on service delivery. While many organisations can be forgiven for not foreseeing the pandemic, the unpreparedness is a concern. So what can organisations do to ensure the new normal learns from the old normal’s mistakes?
For service teams tasked with keeping the lights on in critical areas such as healthcare, utilities and food manufacture and logistics, it has undoubtedly been a challenge. Service engineers still need to fix things and they need tools and parts to do the job. So, should organisations have installed more flexible working structures and supply relationships pre-Covid-19? Should they now look at mixed labour and supply models to cope with the ebb and flow of service demands?
For starters, there is going to be a backlog of machines to fix, especially as a lot of work that was shelved during the lockdown was preventive maintenance. How can organisations get up to speed quickly? The mixed labour model could certainly feature here, with increased use of third-party contractors capable of scaling up or down depending on requirements. A core team of engineers would be supplemented by external support in a crisis. This core team could also work in a flexible way, much in the same way they have done over the past few weeks.
To build resilience, organisations need to ensure that maintenance skills are available regardless of the crisis and this will come down to contingencies built into emergency plans. As well as mixed labour models, this may also include emergency partner plans, alternatives for products and parts to enable a greater chance of supply continuity. Covid-19 has almost certainly forced organisations to re-visit their risk assessments and this may also include customer risk. For example, what is the spread of risk across the customer base? Is one customer dominating and is this customer serviced by one highly skilled engineer? It’s important to identify the dependencies and try and spread the risk.
Overall, what any service supply chain needs is greater flexibility and digital control. Mobile tools and centralised machine histories, remote access to supplier parts ordering and the ability to scale service teams quickly, will go a long way to helping organisations cope with any future crisis, whether it’s economic or health related. But more than that, these are good practises anyway. If Covid-19 has done one thing for service teams, it’s taught them that the new normal is not just about coping and preparing for future disruption, it’s about working better and delivering continuity now.
Sumair Dutta is Industry Analyst and Senior Director of Global Customer Transformation at ServiceMax.